
Sourcing
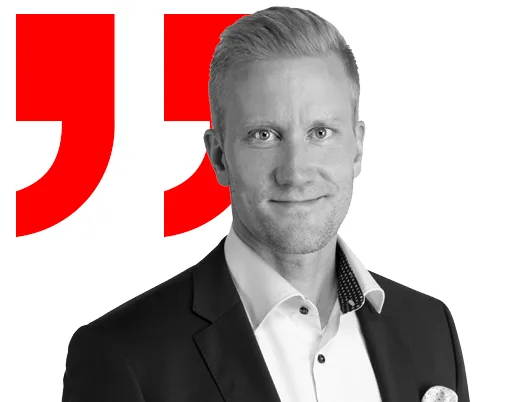
”We are committed to sourcing our products responsibly and respecting human rights.”
When monitoring sustainability, we focus especially on high-risk countries such as China and Bangladesh, where there is, according to the World Bank Worldwide Governance indicators, a higher risk for violations in labour and human rights.
Juha Valtonen, Chief Sourcing and Buying Officer, Tokmanni Group
In developing sustainable sourcing, we focus on the manufacturing of our private label products as well as direct imports from high-risk countries. In these product categories, we have the best opportunities to influence.
We assure the sustainability of our products and operations by visiting factories ourselves and by only purchasing products from factories where a third party has conducted a BSCI audit or equivalent and inspected the working conditions and the fulfilment of employee rights. During our own factory visits, we check the working conditions, product quality and production capacity as well as the factory’s management capacity.
During 2024, Tokmanni Group’s sustainable sourcing practices were integrated into Dollarstore’s operations, and this work will continue in 2025.
In Tokmanni Group’s general terms on purchasing, the requirements of responsible sourcing are defined on a general level.
In our general terms of purchasing, we require suppliers to
1. Comply with applicable international sanctions and act in compliance with anti-money laundering regulations and anti-bribery policies.
2. Comply to the amfori BSCI Code of Conduct principles by signing the amfori BSCI Code of Conduct and to carry out self-evaluations and audits according to amfori code of conduct.
- If the product is manufactured in a high-risk country, we require a factory audit. Approved audit systems for high-risk country factories are amfori BSCI, SA8000, and on a case-by-case basis ICTI, SMETA (4-pillar) and BRCGS.
- For certain raw materials, we also require raw material certification. These raw materials, such as cotton, have significant environmental and human rights risks in their production. Approved raw material certifications are for example GOTS, OCS, Better Cotton, Fair Trade, RSPO, MSC, FSC, PEFC.
3. If requested, the Supplier agrees to supply their carbon footprint information (CO2 emissions) and information about the other environmental impacts of their actions.
In accordance with the guidelines of BSCI, Tokmanni Group has zero tolerance for the following issues: child labour, bonded and forced labour, inhumane treatment, occupational health and safety and unethical behaviour, e.g. an attempt to bribe auditors or falsify information about the supply chain. If such cases occur, Tokmanni Group will freeze the purchases immediately and contact the supplier for further investigation of the problems. After further investigation, each case and the continuation of cooperation with the factory will be evaluated separately.
In the amfori BSCI system, zero tolerance problems are dealt together with all amfori members using the factory, and amfori coordinates this process. Zero tolerance problems are very rare in the factories we use. The most common grievances detected by audits and self-inspections were related to overtime, pay and minor deficiencies in compliance with safety instructions.
Tokmanni Group allows suppliers to use subcontracting, but the subcontracting factories must also be BSCI audited and approved by Tokmanni Group. All factories and subcontractors and their changes must be approved by Tokmanni Group in advance.
Audits to all factories in high-risk countries
We strive to ensure that 100 % of factories’ BSCI audits are valid both at the time of purchase of a specific product and at the time of production with an overall grade of C or better. Sometimes the audit of the factory has not been renewed in time, and thus, 100% coverage is difficult to achieve in practice.
Amfori BSCI is an international system that reviews and audits the realisation of employee rights, the quality of working conditions, and safety issues at factories. In the BSCI audit, several things are assessed in accordance with amfori BSCI Code of Conduct and System Manual, for example fair remuneration, overtime, occupational health and safety, use of forced or child labour and the right of employees to join a trade union. Amfori BSCI audit results are assessed on a five-step scale, using the grades A, B, C, D or E.
Most of our partner factories received a C (acceptable) overall grade. This is not an average number of the 13 performance areas, rather, scoring a D (insufficient) in two and A (very good) or B (good) in rest will bring down the overall grade to a C.
The most common issues found in amfori BCSI audits in the factories we use are generally related to management systems and working times. If the result is a D or a C with significant shortcomings, a corrective action plan with clear timeline is requested from the factories. If the result is D or E (unacceptable), the factory cannot be used until the issues have been solved.
SA8000-audited factories automatically receive a good overall assessment using the amfori BSCI system. Based on case-by-case judgement, the SMETA audits, the toy business’ ICTI Care audits and BRCGS audits for groceries can also be accepted.
In addition to the amfori BSCI audits, we carry out our own factory inspections. All new suppliers are evaluated before the start of cooperation or in the initial phase, and at the same time the need for a factory inspection is evaluated.
A total of 121 own factory assessments and third-party audits in 2024
In addition to the BSCI audits, our own experts conducted 57 (2023: 62) sustainability and quality assessments at partner factories, and 64 (2023: 73) third-party audits in risk countries were conducted.
The most common issues found in these audits involved overtime, social insurance, and minor safety non-compliances. Corrective action plans were required from all factories.
The choice of factories to be inspected is influenced by, among other things, the country’s and industry’s risks, as well as the spend. For example, manual work or the use of migrant workers are risk-increasing factors..
We strive to increase the use of more sustainable cotton, for instance
At the end of 2024, 54.5% (2023: 39%) of our cotton was sourced more sustainably than before. The work to increase the use of more sustainable cotton continues.
Making our supply chain for clothing more transparent
We do not own any factories, as we always work with independent manufacturers. In order to increase supply chain transparency, we disclose all factories that manufacture Tokmanni Oy’s private label clothing, shoes, bags and accessories.
The list includes e.g. names and addresses of factories. Our private label clothing brands include Force New Attitude, Future TT Sport, Peuhu, Pola, Pola Plus, R-Cover, Vaeltaja and Catmandoo. The factory list is updated annually. The latest update was made on August 27th 2024.
Work with amfori BEPI
Amfori’s environmental assessment programme (BEPI) is a business-driven initiative, aimed at improving the environmental performance throughout supply chains. It covers a scope of 11 environmental performance areas ranging from greenhouse gases and water consumption to chemical management.
The first step for the factories is to conduct an amfori BEPI Self-Assessment on their environmental performance. According to the self-assessments conducted so far, our factories need focus on greenhouse gasses, waste management, emissions to air and environmental nuisances. Tokmanni Group has joined the amfori BEPI environmental assessment programme.
Living wage
We respect and demand that our partners respect human rights. We promote human rights, adequate living wages, and appropriate and safe working conditions in our supply chain through dialogue, audits and training.
Living wage is one of the issues that comes up in human rights assessments. We are committed to promoting a living wage for employees in our supply chains. Our products are subcontracted and we do not own factories. Because we do not pay wages in the supply chain ourselves, we cannot influence living wages alone.
Both the amfori BSCI Code of Conduct and our Supplier Code of Conduct contain the principle of fair remuneration, which enables the employee and his family to earn a reasonable living sufficient to meet basic needs. However, local statutory minimum wages or wages under collective agreements are not always sufficient to achieve this goal. We ask about salaries through both our own and BSCI audits and thus stimulate constructive dialogue on the subject at factories. The amfori BSCI audit includes a Fair Remuneration Scan, where workforce’s decent standard of living is calculated. Anker-methodology is normally used.
We also strive to promote living wages together with others, as this can only be resolved through long-term commitment and close cooperation with global and local stakeholders. Key stakeholders include other companies, legislators, local trade unions and other employee representatives. We are a member of amfori BSCI and support their initiatives that aim to achieve living wage in supply chains.
One channel for living on a wage in high-risk countries would be freedom of association and collective bargaining. Raising the national minimum wage would effectively promote living wages.
Discover more
Which sustainability topics would you like us to tell more about?
Tell us, for example, via Tokmanni’s customer service, we would like to hear from you!