
Quality assurance
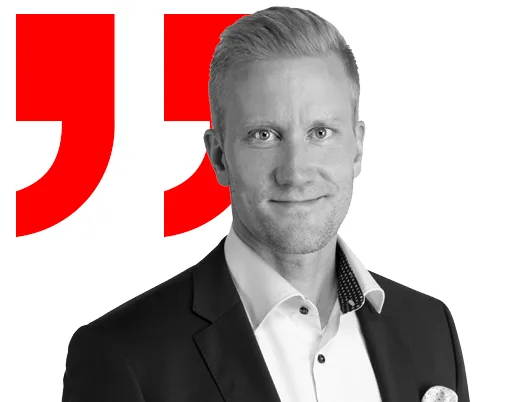
“Product quality and safety are are among our most important things.”
We aim to ensure that all products we sell are safe to use and of high quality. We are responsible for ensuring the safety and legal compliance of the products we sell.
Juha Valtonen, Chief Sourcing and Buying Officer, Tokmanni Group
Product quality is part of sustainability and means product safety, legality, durability and customer experience to us.
Product quality is important to us, and we work hard to ensure it.
Our quality department in Mäntsälä in Finland takes care of, for example, the regulatory compliance of the products we sell, the labelling of packaging, the definition of quality criteria, and testing various products. Dozens of new products and finished product quality inspection reports from tools to toys are inspected daily. Our sourcing office in Shanghai in China also has its own quality team. This enables us to react to possible quality deviations in good time before the goods leave from the manufacturing countries.
At our own factory social compliance inspections, focus is placed also on product quality and quality management.
We are responsible for the correctness of the texts and packaging labels of the goods we sell. All our private label brand products state the country of manufacture and the recyclability of the packaging materials. We reviewed or renewed 6,986 private label entries in 2024 (2023: 5,004). We also have products tested by third parties.
We measure product safety and the quality of experience in terms of the number of product types that do not meet all our requirements. In 2024, we identified 23 (2023: 23) such cases, most of which were due to poor product quality detected through self-monitoring or customer returns.
There are also a few decisions to stop selling goods due to possible non-compliance every year. In 2024, Tokmanni Group carried out one market withdrawal procedure for its own brands or imported brands. The product was a chocolate chip cookie, with Tokmanni acting as the distributor for the Dutch manufacturer. During the manufacturing process, a production device had broken, potentially contaminating the batch with metal fragments.
Chemicals
We want to ensure that our products are safe and do not contain unwanted chemicals. We are committed to complying with EU chemicals legislation and require the same from our suppliers. We also strive to avoid harmful chemicals in our products by identifying harmful chemicals in our products and then restricting their use or substituting them. We are, for example, committed to substituting substances of very high concern (SVHC) with less harmful chemicals. If is not possible to substitute these, the product will not be sold.
The amfori BEPI environmental programme helps us to manage the chemicals in the production chain. We also restrict certain chemicals in cargo container gases and desiccants. In addition, depending on the product type, we require suppliers to submit chemical test reports and have a list of banned chemicals in textiles that is stricter than the legislation. The list covers both chemicals in clothing and chemicals used in production. For instance, perfluorinated compounds, nonylphenol ethoxylates and azo dyes are excluded form use.

Case: Products and Sourcing | A product’s quality assurance journey at Tokmanni variety discount retail chain
Tokmanni’s quality control process is extensive. Once we identify a new product that we wish to offer our customers, we begin the search for a supplier. When possible, we choose suppliers we have already worked with before.
Once potential suppliers have been identified, the factories send samples of the new product to Finland. The product’s quality is tested by an independent partner. The supplier is then selected based on criteria such as quality-price ratio and supply reliability. We only select products with high quality standards. If possible, a Tokmanni representative visits the factory before the final decision.
After the supplier has been chosen and production begins, an independent quality control partner inspects each product batch before it is shipped to Finland. Once the products arrive at our central warehouse, a quality specialist checks them on-site.
Our office in Shanghai
Our Shanghai office in China makes sure that the products we procure are up to our high standards. With the help of the Shanghai team, Tokmanni can ensure the quality and sustainability of our products, even when manufactured on another continent.
The Shanghai office has 33 employees in total, and it houses two teams: the commercial team and the quality and compliance assurance team. In 2021, Tokmanni increased the number of quality and compliance employees at the Shanghai office from three to five.
In practice, the Shanghai team’s quality assurance operations include factory checks and ensuring timely delivery. Factory checks are conducted at potential new suppliers’ factories and at factories where the risks of human rights violations are the highest.
“Because of our local team, we have been able to ensure quality, responsibility and logistical flow also during these challenging times. This is a clear advantage compared to other operators,” says Mikko Kalmi, Quality Manager at Tokmanni.
In 2021, Tokmanni’s buyers further increased communication and collaboration with the Shanghai office to ensure product quality.
Further improvements in quality assurance
Next, Tokmanni will be focusing on improving supplier information management and identifying supplier risk. We are committed to continuous improvement in every aspect of our business, including quality control.
This article was published in early 2022.
Which sustainability topics would you like us to tell more about?
Tell us, for example, via Tokmanni’s customer service, we would like to hear from you!